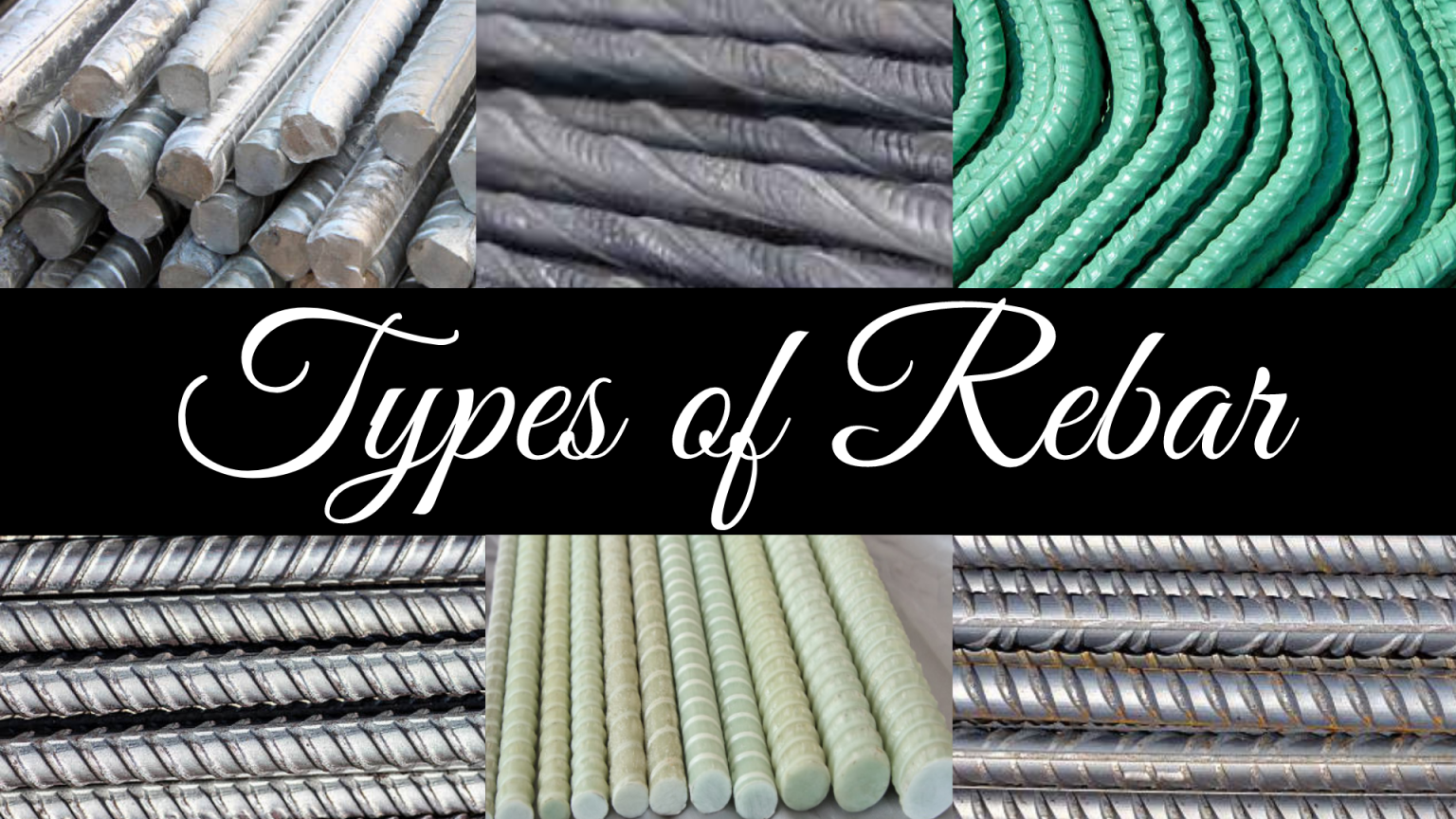
WHAT IS REBAR?
Rebar is a type of reinforcing bar that is used to strengthen the tensile strength of concrete and is generally composed of steel. As we all know, concrete is reasonably strong in compression but extremely weak in tension. The overall performance of concrete structures under loaded situations is improved by adding reinforcement. In this article, we’ll go through the many types of rebar that are used in steel reinforcement.
Types of Steel Reinforcement Bars
The following are the most common types of steel bars used in construction:
1.MILD STEEL BAR
The surface of the mild steel bars is plain and circular in shape. They come in different sizes, ranging from 6 mm to 50 mm. They are used in concrete for a variety of functions, including dowels at expansion joints where bars must move in a metal or paper sleeve, contraction joints in highways and runways, and column spirals. They are easy to cut and bend without causing damage. Mild steel bar is not suggested for structural constructions such as bridges and other large structures owing to poor bonding between concrete and steel, slippage, and strength. Steel that exceeds the minimum ultimate tensile strength of 550 n/mm2 and 10000 N/mm2 is classified as medium-tensile steel or high-tensile steel.
Mild steel is divided into two grades: Grade I and Grade II. The mechanical characteristics of mild steel bars are as follows:
2. DEFORMED STEEL BAR
The surface of deformed steel bars has ribs, lugs, and other deformations that strengthen the binding strength between steel and concrete.
Tensile, yield, and bond strength are all high in deformed bars. Hooks are not required at the ends of deformed bars since their bond strength is higher than that of regular mild steel bars.
Types of Deformed Steel Bars
There are two types of rebar for deformed steel bars.
A. TMT Bars (Thermo Mechanically Treated Bars)
TMT is a sophisticated technique that involves quenching red-hot rebars with a sequence of water jets, resulting in a hardened outer layer surface enclosing a softer core. The TMT bar is the most recent innovation in the steel industry. These types of rebar are commonly used as reinforcement in the construction of buildings, roads, bridges, and other construction projects.
Characteristics of TMT Bars
- Better ductility and malleability
- High yield strength and toughness
- More bonding strength
- Earthquake resistance
- Corrosion resistance
- High thermal resistance
- Economical and safe in use
- No loss in strength at welded joints
- Ordinary electrodes used for welding the joints
B. Cold Twisted Bar
Cold twisted bars (CTD) are high-strength deformed bars (HSD) whose quality is enhanced by different cold working procedures (stretching and twisting). CTD bars have a yield stress that is 50% higher than conventional mild steel bars. These rebars come in diameters ranging from 4mm to 50mm. This type of rebar generates higher operating stresses while utilizing less steel. Due to cold twisting, there is surface stress and visible fissures, which results in decreased ductility, increased corrosion rate, and a drop in elongation percent of 24 to 13 percent. Buildings, highways, bridges, water-retaining structures, precast concrete, and other concrete constructions frequently use these bars as reinforcement.
Characteristics of Cold twisted bar
- Low carbon content- Lower carbon content makes it ductile.
- Welding capabilities-Due to the decreased carbon value, welding is feasible.
- Less steel consumption- Construction with these bars consumes 30-40% less steel compared to other types of rebars.
- Economical- As it consume less steel it is economical.
- Better functional aspects and structural safety.
- High tensile strength- CTD bars possess high tensile strength
3. Carbon Steel Bar
Due to its carbon color, this is the most popular variety of carbon steel rebar, also known as a black bar. One notable disadvantage is that it corrodes quickly, making it unsuitable for use in high-humidity environments or constructions that are constantly exposed to water. Carbon steel rebars, on the other hand, are an excellent choice for all other sorts of constructions.
4. Epoxy Coated Rebar
Epoxy coated rebar, often known as green rebar, is utilized in concrete that is exposed to corrosive environments.
To strengthen the concrete and prevent it from corrosion, epoxy-coated rebar or corrosion-resistant rebar is used instead of traditional reinforcing bars. To ensure corrosion resistance, the epoxy coating is added to the steel at a factory prior to shipping. Corrosive concrete can benefit from the use of epoxy-coated steel reinforcing bars (rebar). Exposure to deicing salts or seawater is one example. This bar is suitable for usage in maritime construction, bridge infrastructure, buildings, and roads, etc.
5. Stainless steel rebars
These types of rebar are some of the best types of rebar for applications requiring strong corrosion resistance or where restoration is difficult and expensive. However, epoxy-coated rebar is at least eight times more expensive. Stainless steel rebars provide a number of benefits.
- Extremely long-lasting and durable
- Black bars are 1500 times more corrosive than white bars.
- There’s no need to maintain it.
- Will not be harmed during transit or installation.
6. Galvanized Rebars
A protective covering of zinc metal is applied to this rebar. The corrosion resistance of galvanized rebars is 40 times that of carbon steel rebars. They are, nevertheless, more expensive than black bars. These bars are ideal for construction that will be exposed to heavy levels of moisture and humidity.
7. European Rebars
These rebars are often made of manganese, which makes them easily flexible. European rebars are not suited for use in locations prone to extreme weather and natural disasters like tornadoes, earthquakes, and hurricanes.
8. Glass-Fiber –Reinforced-Polymer Rebars (GFRP)
Fiberglass rebars are also known as fiberglass-reinforced polymer rebars. Carbon fiber is commonly used. GFRP has a number of benefits, including:
- It will never corrode due to exposure to salts or other environmental factors.
- The tensile strength of these bars is greater than that of steel.
- Non-conductive electrical properties and thermal insulator capabilities outperform steel rebar.
- Due to its lighter weight, it saves money on material handling and transportation.
9. Welded Wire Fabric
Carbon steel wires are placed at 90 degree angles and welded at all intersections to create this type of
rebar. The design will resemble a square grid or mesh. WWF is perfect for well-compacted floor slabs, sidewalks, highways, culverts, small canals, runway pavements, and concrete pads.
BEAM REINFORCEMENT DETAIL
Detailing is among the most important aspects of any building. The engineer should carefully analyze and install the various RCC components.
To ensure a faultless building process, proper detailing of reinforcements with correct designs is required at the construction site. Typically, these designs include a timetable for bar bending. The bar bending schedule specifies the length and number of bends, as well as their position and form. The detailing of beams is normally related to the following:
- Bar size and number (or spacing)
- Bar lap and curtailment (or bending)
- Expansion of bar length
- Chair bars and spacers
- The reinforcement has a clear cover.
The steel used in beams is divided into several groups depending on the relevant objectives:
1. At the compression and tension faces, there is longitudinal reinforcement.
2.Vertical stirrups and/or bent-up longitudinal bars can be used as shear reinforcements.
- When a beam’s web depth reaches 750 mm, side face reinforcement is added to the beam’s web.
- Distribute at least 0.1 percent of the web area evenly on two faces, separated by no more than 300 mm or the web thickness, whichever is less.
According to ACI 318M-14, spacing of transverse reinforcement (stirrups) in location of the spliced rebar must not exceed the lesser of D/4 and 100mm where D is the depth of the beam.
Length of extra bars and splice.
Proper splicing of Longitudinal Rebars