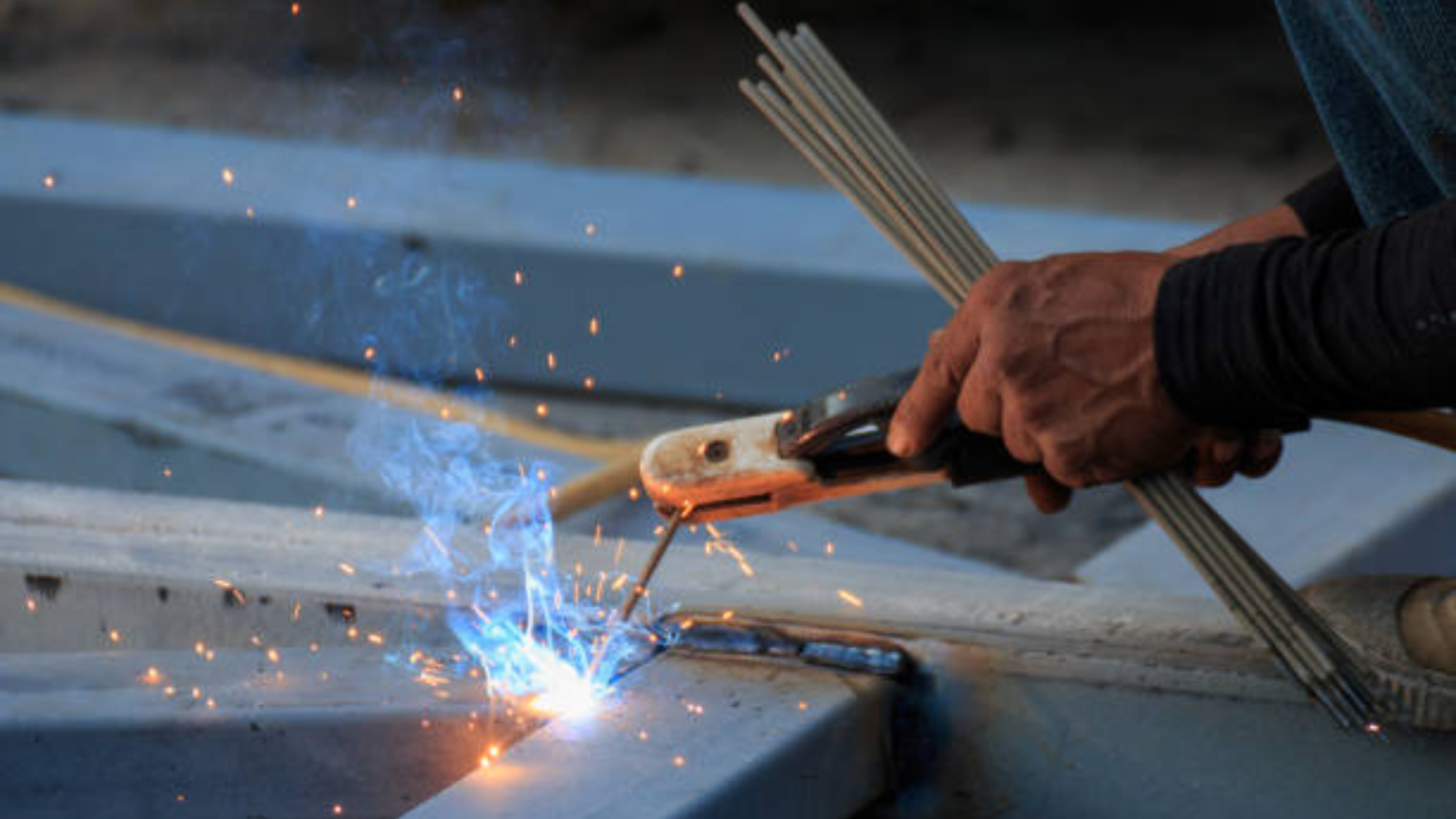
A welding joint refers to the point where two or more pieces of material are joined together by the process of welding. It is the area where the welding operation takes place, and the joint must be properly prepared and positioned to ensure a strong and durable weld.
The welding joint can vary in shape, size, and configuration depending on the type of welding process, the materials being joined, and the intended application of the welded structure. Different joint designs are used to accommodate the specific requirements of the weld, such as strength, appearance, and resistance to stress or corrosion.
Types of Welding Joints
There are several types of welding joints commonly used in various welding processes. Here are some of the most commonly used welding joints:
Butt Welding Joints
A butt welding joint is a type of joint used to join two metal pieces along their edges in a straight line. It involves the fusion of the two metal surfaces to form a continuous weld. Butt joints can be used to join similar or dissimilar metals, depending on the welding process and the materials involved.
Welding Styles for Butt Joint
- Bevel-Groove Butt Weld
- J-Groove Butt Weld
- Flare-Bevel-Groove Butt Weld
- U-Groove Butt Weld
- Flare-V-Groove Butt Weld
- Square-Groove Butt Weld
Corner Welding Joints
A corner welding joint is a type of joint where two metal pieces are joined at a right angle, forming a corner. This type of joint is commonly used in welding applications, particularly in structural and fabrication work. Corner joints can be found in various industries, including construction, manufacturing, and metalwork.
Welding Styles for Corner Joint
The welding style for a corner joint depends on several factors, including the material being welded, joint thickness, welding process, and the desired strength and appearance of the joint. Here are some common welding styles used for corner joints:
- Edge Weld
- Bevel-Groove Weld
- Corner-Flange Weld
- Flare-V-Groove Weld
- Spot-Weld
- Fillet Weld
- J-Groove Weld
- V-Groove Weld
- Square-Groove Weld or Butt Weld
- U-Groove Weld
Tee Welding Joints
Tee welding joints, also known as T-joints, are a type of joint used to join two metal pieces at a right angle, forming a âTâ shape. It is commonly used in welding applications where one piece of metal is welded perpendicularly to the surface of another piece. Tee joints can be found in various industries, including construction, fabrication, and metalwork.
Welding Styles for Tee Joint
When it comes to welding tee joints, several welding styles can be employed based on the specific welding process and materials involved. Here are some common welding styles for tee joints:
- Bevel-Groove Weld
- Fillet Weld
- J-Groove Weld
- Flare-Bevel-Groove Weld
- Plug Weld
- Slot Weld
- Melt-Through Weld
Edge Welding Joints
Edge welding joints, also known as edge joints, are a type of joint used to join two metal pieces along their edges in a straight line. Unlike a butt joint, where the metal pieces are joined end-to-end, in an edge joint, the edges of the metal pieces are aligned and welded together. Edge joints are commonly used in welding applications, particularly in sheet metal fabrication and thin metal joining.
Welding Styles for Edge Joint
When it comes to welding edge joints, several welding styles can be used depending on the specific welding process and materials involved. Here are some common welding styles for edge joints:
- Bevel-Groove Weld
- Edge-Flange Weld
- Corner-Flange Weld
- J-Groove Weld
- U-Groove Weld
- V-Groove Weld
- Square-Groove Weld or Butt Weld
Lap Welding Joints
Lap welding joints, also known as lap joints, are a type of joint used to join two metal pieces by overlapping them. In this joint, one piece of metal is placed over another, and the weld is applied along the overlapping region. Lap joints are commonly used in welding applications, particularly in sheet metal fabrication and joining thin metal plates.
Welding Style for Lap Joint
The welding style for a lap joint can vary depending on factors such as the material being welded, joint thickness, welding process, and desired strength and appearance of the joint.
- Flare-Bevel-Groove Weld
- J-Groove Weld
- Bevel-Groove Weld
- Slot Weld
- Plug Weld
- Spot-Weld
Advantage of Welding Joint
Welding joints offer several advantages over other methods of joining materials. Here are some of the key advantages of welding joints:
- The welded joint has a high strength, sometimes greater than the parent metal. The welded joint cannot be easily failed by using the same or less amount of material that was used in either piece of metal prior to welding. When two different materials are welded, their properties combine to produce a high-quality weldment that is more effective and durable than the two original pieces. Typically, the welded joint is stronger than the parent metal.
- Welding can be performed using a variety of materials, including mild steel, stainless steel, alloy steel, and other metals. Therefore, due to their high demand, various types of welding processes are needed to produce various kinds of components to meet various needs in industries. Welding is a simple way to join metals and is one of the most versatile joining processes. It can join metals in all directions, which other welding processes cannot.
- Has the ability to manufacture heat-resistant materials such as alloy steel and stainless steel.
- Components are simple to mass produce and save material.
- Capable of creating complex structures
- There is no need for machining after welding, which saves time and money; additionally, the quality is more accurate, and close tolerances can be achieved.
- It is appropriate for high production and reduced product liability.
- It is appropriate for large components, bulky parts, and high-quality demands.
- Welding efficiency can be increased successfully by using robots or automated systems to perform the task of welding automatically and quickly.
Also Read:
Disadvantage of Welding Joint
While welding joints offer numerous advantages, there are also some disadvantages to consider. Here are a few common disadvantages associated with welding joints:
- It is limited in size. It makes it difficult to maintain control over the thickness of the material.
- A complex process.
- It is not appropriate for a large sheet of metal.
- Welding can generate sparks, which can ignite a fire.
- Welding small items is simple, but welding large items is more difficult.
- Welding experience is required for better outcomes. Because heating and cooling can degrade metal quality, the process must be carried out by an expert.
- Welding fumes are unsafe, and protective clothing and masks are required.
- Some materials cannot be welded.