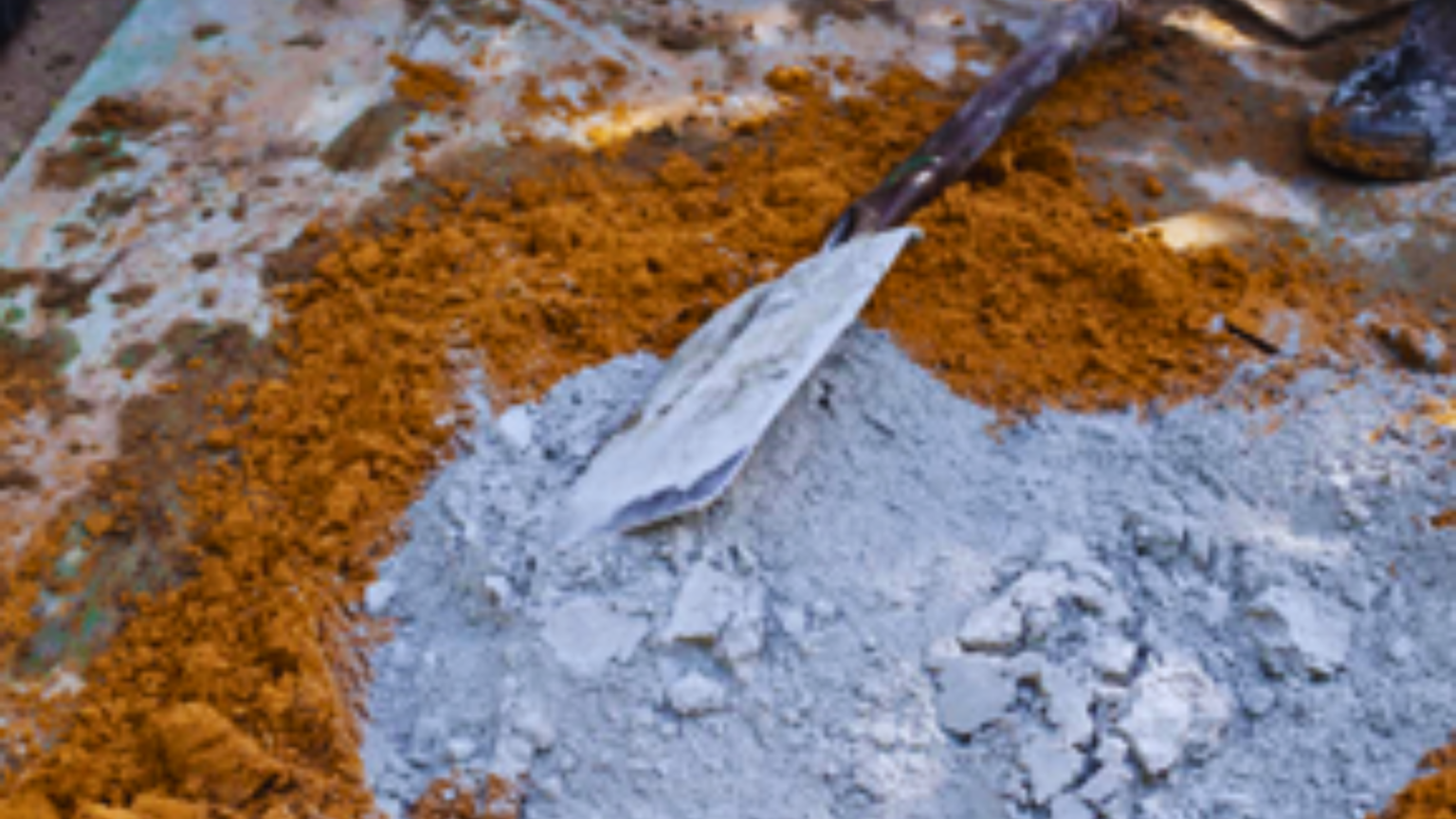
What is Soil Cement?
Soil-cement is a construction material that is made by mixing soil, cement, and water together to create a hardened, compacted material suitable for use in various engineering and construction applications. It is commonly used for stabilizing and strengthening soil to create a durable and cost-effective base for roads, pavements, airstrips, and other infrastructure projects.
The process of creating soil cement involves blending the native soil with Portland cement, which is a fine powder that reacts with water to form a cementitious binder. The amount of cement used depends on the characteristics of the soil and the desired strength of the final product.
Composition of Soil Cement
The composition of soil cement typically includes three main components: soil, cement, and water. The proportions of these components can vary depending on the specific engineering requirements of the project and the properties of the available materials. The following is a general guideline for the composition of soil cement:
Soil
- Soil TypeThe soil used in soil cement should generally have a high content of fines, including clay and silt, as these particles help in providing cohesion and binding with the cement.
- Particle Size DistributionA mix of different particle sizes, including fine and coarse particles, contributes to the overall strength and stability of the soil cement.
- GradationThe gradation or particle size distribution of the soil should be evaluated to ensure optimal compaction and mechanical properties.
Cement
- TypePortland cement is commonly used for soil cement. It is a hydraulic cement that reacts with water to form a strong cementitious binder.
- ContentThe amount of cement added to the mixture is typically between 3% to 10% by weight of the dry soil. The exact percentage depends on factors such as soil characteristics and intended strength.
Water
- Water-Cement RatioThe water content is controlled to achieve a specific water-cement ratio, which affects the workability, strength development, and curing of the soil cement.
- Moisture ContentThe soil-cement mixture should be at the optimum moisture content for compaction, ensuring proper compaction and cement hydration.
Manufacturing Process of Soil Cement
The manufacturing process of soil cement involves several steps to create a strong and durable construction material by blending soil, cement, and water. The process can vary depending on the specific project requirements, equipment availability, and local conditions. Here’s an overview of the typical manufacturing process:
Material Selection and Preparation
- Soil SelectionChoose a suitable soil that has a high percentage of fines (clay and silt) and meets the engineering requirements of the project.
- Cement SelectionSelect an appropriate type of cement, typically Portland cement, based on its compatibility with the soil and project specifications.
- PreparationIf necessary, the soil may undergo preliminary processing, such as grading, screening, or pulverizing, to achieve the desired particle size distribution.
Mixing
- Batch MixingIn small-scale projects, soil and cement can be mixed in batches using equipment like a portable concrete mixer. The soil and cement are combined in predetermined proportions based on engineering design.
- Continuous MixingLarger projects may use specialized continuous mixing equipment. Soil and cement are continuously fed into the mixer, ensuring a consistent mixture.
Adding Water
- Water ContentDetermine the optimal water content based on the moisture-density relationship of the soil. This is critical for achieving proper compaction and cement hydration.
- Water-Cement RatioControl the water-cement ratio to ensure adequate cement hydration without making the mixture too wet.
Mixing and Blending
- The soil, cement, and water are mixed thoroughly to create a homogenous mixture. This can be done using mechanical mixers or specialized soil-cement mixing equipment. The mixing process should ensure even distribution of cement particles throughout the soil matrix.
Compaction
- Place the mixed soil-cement material in the desired location, such as a roadbed or foundation. Compact the material using heavy rollers, compactors, or other compaction equipment. Compaction removes air voids, increases density, and improves the material’s strength.
Curing
- Allow the compacted soil cement to cure for a specified period. This could be several days or weeks, depending on the project requirements. Curing allows the cement to hydrate and form strong bonds with the soil particles, enhancing the material’s strength and durability.
Quality Control and Testing
- Perform laboratory tests on samples to verify the strength, density, and other engineering properties of the soil cement. Adjust the manufacturing process or mixture proportions as needed based on test results.
Final Application
- Once the soil cement has cured and achieved the desired strength, it can be used as a stable base for road construction, pavements, building foundations, and other applications.
- Throughout the manufacturing process, it’s important to monitor and control factors such as mixing time, compaction effort, and curing conditions to ensure the desired quality and performance of the soil cement. The exact procedures and equipment used can vary based on the project’s scale and requirements.
Types of Soil Cement
There are several types of soil cement, each designed to meet specific engineering and construction requirements. These types can be differentiated based on factors like the type of soil, cement content, additives, and intended applications. Here are some common types of soil cement:
Soil Cement Base
A Soil-Cement Base (SCB) is a construction material that combines soil, cement, and water to create a strong and durable foundation layer for various infrastructure projects. SCB is commonly used in road construction, highways, airports, and other transportation-related applications. It provides a cost-effective and sustainable solution for creating stable load-bearing surfaces.
Soil-Cement Base serves as a robust and reliable foundation for subsequent construction layers such as asphalt or concrete pavements. Proper design, compaction, and curing practices are essential to ensure the successful performance of Soil-Cement Base in construction projects. It offers a sustainable and cost-effective solution for creating stable and durable surfaces in transportation and infrastructure development.
Cement Modified Soil (CMS)
Cement-modified soil refers to a construction material created by blending soil with a certain amount of cement to enhance its engineering properties. This mixture is widely used in civil engineering and construction projects to improve the strength, durability, and performance of the soil for various applications. Cement-modified soil is commonly used as a base or subbase material in road construction, pavements, building foundations, and other infrastructure projects.
Cement-modified soil is adaptable to various project requirements and can be designed to meet specific engineering standards. It offers a sustainable and economically viable solution for infrastructure development, particularly in areas where suitable construction materials are limited or costly. Proper design, compaction, and curing practices are essential to ensure the successful performance of cement-modified soil in construction projects.
Cement Treated Base (CTB)
A cement-treated base (CTB) refers to a construction material produced by mixing granular base materials, such as aggregate or soil, with a certain amount of cement to enhance its strength, durability, and load-bearing capacity. CTB is commonly used in road construction and other infrastructure projects as a stable and solid foundation for pavements, highways, and other structures.
Cement-treated base is a cost-effective solution for creating a stable foundation in road construction and other infrastructure projects. It provides a reliable base that can withstand heavy loads and traffic, contributing to the longevity and performance of the overall structure. Proper design, compaction, curing, and quality control practices are essential for ensuring the success of a cement-treated base in construction projects.
Acrylic Copolymer
An acrylic copolymer is a type of polymer that is formed through the copolymerization of different acrylic monomers. Copolymerization involves the combination of two or more distinct monomers to create a polymer with specific properties tailored to particular applications. Acrylic copolymers are widely used in various industries due to their versatility, durability, and a range of desirable characteristics.
Acrylic copolymers are commonly employed in the production of paints, coatings, adhesives, textiles, and other materials. They can be tailored to exhibit a variety of properties, making them suitable for diverse applications. Different types of acrylic copolymers can be synthesized by adjusting the types and proportions of monomers used in the polymerization process.
Also Read: Types of Skirting | Factors Affecting Concrete Strength | Dewatering Methods in Construction
Advantages
- A wide range of resources
- Maintenance costs are lower.
- Low-cost and highly economical
- Greater weather resistance and strength
- Soil swelling can be reduced.
- It can be used for minor projects.
Disadvantages
- The amount of water must be checked.
- The formation of cracks
- Unsuitable for some soils
- Proper supervision is required.