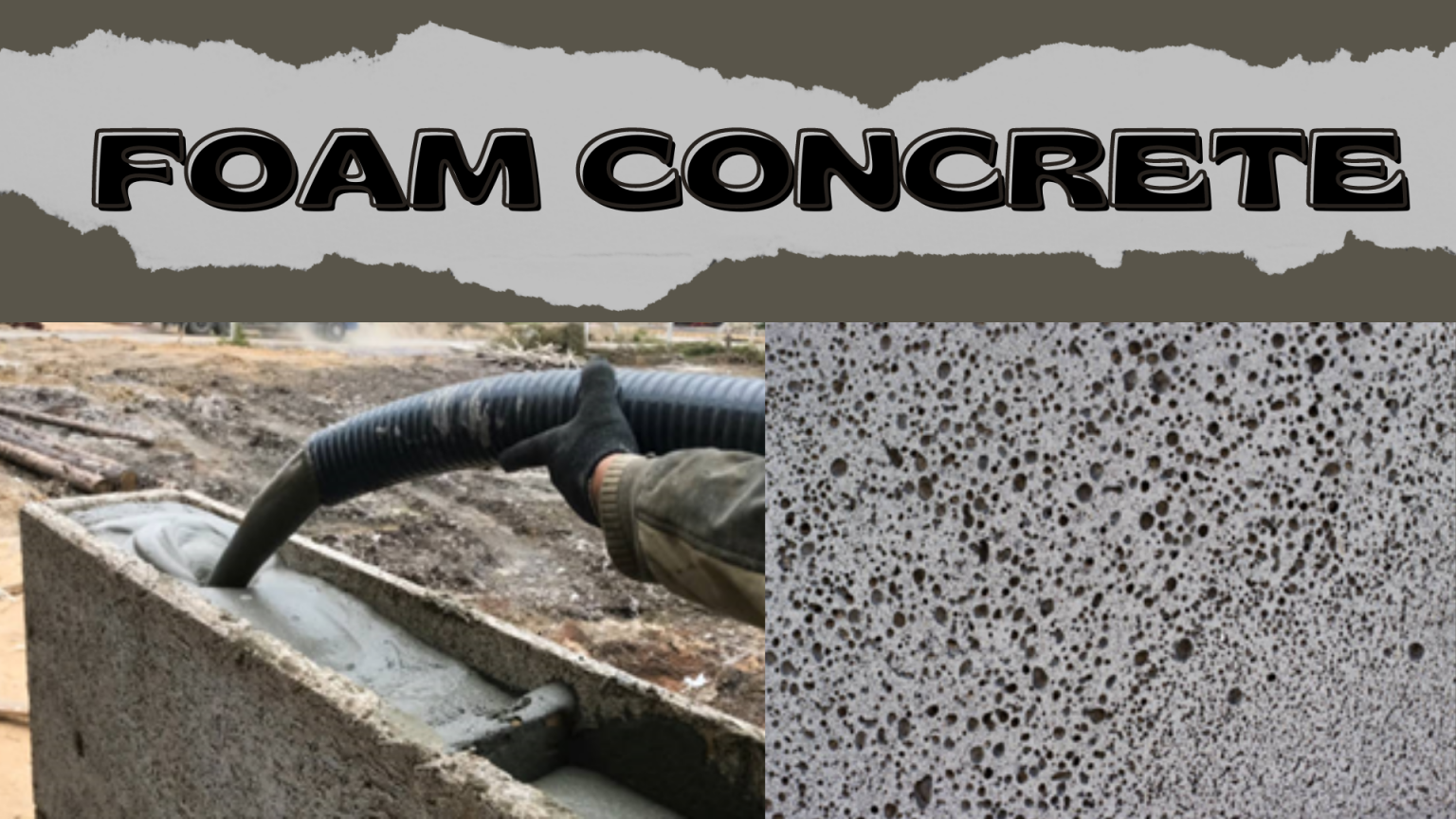
What is Foam Concrete?
Foam concrete is a fantastic material for producing large quantities of relatively low-strength void-filling material; it can be easily pumped long distances and it will fill most cavities.
Since foam concrete is so fluid and flowing, it can “search” without needing to be leveled or compacted. In addition, foam concrete can flow through trenches and enclose pipes, fittings, and other obstructions. For example, foam concrete is modified to reduce loadings, reduce site delivery numbers, and also provide temporary, stable material for work.
Why is it called foam concrete?
A foam concrete is defined as a highly air-entrained sand cement or a cement-only slurry containing more than 20% air by volume. “Propump’s foam mixes range from 20% to 85% by volume and are defined as “a cementitious material that contains at least 20% foam”. Propump’s material contains at least 50% foam by volume.
Using a pre-formed foam, air is mechanically entrained into the cementitious base material to create a lighter density mixed material.
Foam concretes are typically produced on-site with at least 50% by volume air entrainment and up to 85% depending on the mix. Their densities range between 400kg/m3 and 1800kg/m3, and their strengths range between 0.5n/mm2 and 12n/mm2.
The term “foam concrete” can be a little misleading; instead, foamed mortar or foamed grout would be a better description. Other common names include “aerated lightweight concrete” and “cellular lightweight concrete,” to name but just a few.
Production of Foam Concrete
Foam concrete is made by diluting a surfactant in water and passing it through a foam generator, which produces stable foam. The foam is mixed with cementitious mortar or grout to produce a foamed quantity of the required density. These surfactants are also used to make low-density fills. This is also known as controlled low-strength material (CLSM). To achieve an air content of 15 to 25%, the foam is directly added to a mix of low cement content and rich sand. Low density fillers are sometimes sold by manufacturers as foamed concrete, so caution must be taken to avoid misrepresentation.
Foamed concrete is produced using two main methods:
- Pre-foam Method
- Inline Method
Pre-foam Method
This method of making foam concrete can be done on-site or off-site. Foam concrete is made by partially filling a standard ready-mix concrete truck with foam, then mixing the material with the blades inside the “drum.” Pumping would be performed as a secondary operation.
Advantages
- Can be manufactured off-site
- Only requires a basic foam generator
- Ideal for jobs that require little foam.
Disadvantages
- The mixing quality depends on the mixing blades on the truck.
- “Over foaming” is required because volume will be lost during mixing and pumping.
- Densities recorded prior to pumping will differ from those delivered.
- If there are any density issues, changing the foam material in the middle of a load is difficult.
- Inefficient method of delivering materials to the job site. Many deliveries are required, and the timetable is only half full.
- Expensive in the long run due to ready mix suppliers’ part load charges
Inline Method
Inline foam concrete manufacturing can produce both light-weight and high-density foam concrete. Ready-mix trucks with full payloads of material will be delivered to the job site. The inline foam generator and pumping system will pump the neat, base material into the concrete lines while injecting the foam under pressure. This material will then be mixed through a series of in-line mixer plates
Advantages
- To reduce the total number of deliveries, only full mixer deliveries are made.
- There are no part-load charges for uncarried materials.
- Complete foam manufacturing and pumping system
- Continual density adjustment (if necessary, throughout a single load)
- Materials can be manufactured from constituent parts on-site (on-site silo batching).
- It is capable of providing a separate pre-foam solution if necessary, resulting in overall faster production and delivery of finished goods.
Disadvantages
- Expensive, custom-made machinery is required.
- Operating and maintaining equipment can be costly.
Also Read: Concrete Stairs Reinforcement Details
Why is there no aggregate or stone in foam concrete?
To produce a uniform, homogeneous product, the material must be thoroughly mixed with minimal “drop out” or segregation of aggregates. Stones and other large aggregate would simply fall to the bottom of the mix with the addition of high volumes of air and water, resulting in a huge deviation of combine components and therefore an inadequate finished product With a maximum sand thickness of 5 mm, all of the binder and filler remain suspended around the foam as the cement hydrates and begins to cure.
Base mixes for foam concrete
In contrast to traditional “concrete,” the base mixes for foam concrete consist of sand, cement, and water.
The cementitious content is either CEM1 or Ordinary Portland Cement, but cementitious materials such as pulverized fuel ash and ground granulated blast-furnace slag can also be used in varying amounts, depending on the local availability as well as the reaction level to the various foaming agents used.
Why is there so much cement in foam concrete?
When compared to a standard “concrete” mix for slabs or even structural concrete, a foam concrete base mix will have a much higher cement content (minimum 350kg/m3 – 1200kg/m3). There are two reasons for this.
- Air significantly reduces the strength of concrete.
- Water linearly reduces the strength of concrete.
In order to be pumpable and mix with foam, a foam concrete mix will typically have a higher water content than traditional concrete. Additionally, historically, foaming agents and water-reducing or plasticizing agents did not mix well.
Before foaming, a surfactant or foaming agent must be diluted in water; a typical expansion for a protein-based “dry” foam is 20 x. To create a stable foam matrix, the foaming agent is diluted with water at 3% to 5% before being agitated with a “cigar.”
Applications of Foam Concrete
Due to its special characteristics, including density reduction, high flowability, self-compacting concrete, low thermal conductivity, simplicity of production, and relative affordability, foamed concrete can be used in a variety of civil and structural construction.
For example, low-density foamed concrete is used for cavity filling and insulation, whereas high-density foamed concrete is used in structural applications.
Additionally, this concrete is used to create lightweight blocks, pre-cast panels, trench restoration, soil stabilization, fire insulation, thermal and acoustic insulation, as well as shock-absorbing barriers for airports and regular traffic.
Due to its flowability, it is also a great material for voids like those left by old sewage, storage tanks, basements, ducts, and voids under highways brought on by a lot of heavy rain.
Also Read: Types of Concrete Finishes
Advantages of Foam Concrete
- The foam concrete mixture will not settle. As a result, no compaction is required.
- Because concrete is lightweight, the dead weight is reduced.
- In its fresh state, foamed concrete has a freely flowing consistency. This characteristic will aid in completely filling the voids.
- The foam concrete structure can spread and distribute loads extremely well.
- Foamed concrete has no significant lateral loads.
- The capability to absorb water
- Because foam concrete batches are easy to produce, quality control and inspection are straightforward.
- Foam concrete is more resistant to freezing and thawing.
- Work is completed more safely and quickly.
- Low maintenance and cost effectiveness
Disadvantages of Foam Concrete
- Because of the presence of water in the mixed material, foam concrete is extremely sensitive.
- Difficulty in completing
- Longer mixing time.
- Compressive and flexural strength decrease as density increases.