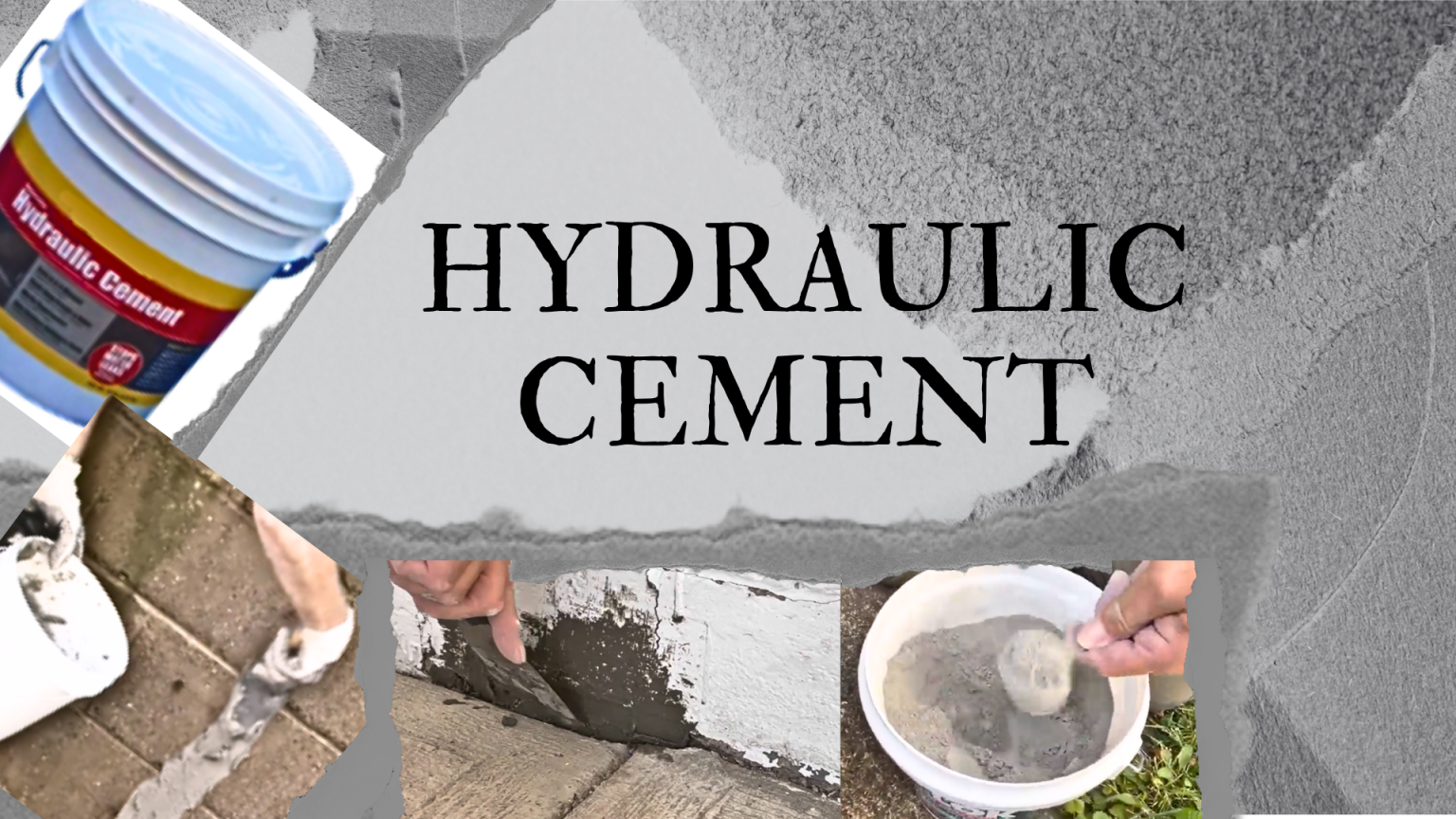
What is Hydraulic Cement?
Hydraulic cement is a type of cement that sets and hardens through a chemical reaction with water, known as hydration, rather than relying solely on air drying. It is called “hydraulic” because it has the ability to set and harden even underwater or in wet conditions.
The key component of hydraulic cement is Portland cement, which is made from a mixture of limestone, clay, and other materials. During the manufacturing process, the raw materials are finely ground and then heated in a kiln to form clinker. The clinker is then ground into a fine powder, which is the Portland cement.
When hydraulic cement is mixed with water, the chemical compounds in the cement react with the water molecules, resulting in a process called hydration. This chemical reaction produces various compounds, such as calcium silicate hydrates (CSH) and calcium hydroxide, which contribute to the hardening and setting of the cement.
Unlike non-hydraulic cements, which rely on air drying and can only harden in dry conditions, hydraulic cement can set and harden even in the presence of water. This property makes it particularly useful for applications such as underwater construction, repair of structures exposed to water or moisture, and in situations where a fast-setting cement is required.
Importance of Hydraulic Cement
Hydraulic cement holds significant importance in various construction and repair applications due to its unique properties. Here are some of the key reasons why hydraulic cement is important:
Setting and hardening in wet conditions
One of its primary advantages is its ability to set and harden even in the presence of water or moisture. This feature makes it ideal for applications such as underwater construction, repairing leaking pipes, and sealing cracks in foundations or basements.
Rapid Setting
Hydraulic cement typically has a faster setting time compared to non-hydraulic cement. This makes it ideal for situations where quick repairs or construction are necessary, such as emergency repairs, infrastructure maintenance, or projects with tight deadlines.
Structural stability
The chemical reaction that occurs during hydration produces calcium silicate hydrates (CSH), which contribute to the binding and hardening of the cement. This results in improved structural stability and resistance to cracking, enhancing the longevity of the constructed or repaired elements.
Versatile applications
Hydraulic cement finds application in various construction and repair projects. It is commonly used for patching and sealing cracks, anchoring bolts and posts, creating watertight seals, and repairing deteriorated concrete structures. Its versatility allows it to be used in different settings, ranging from residential and commercial buildings to infrastructure projects.
Cost-effective solution
Hydraulic cement offers cost advantages due to its fast-setting nature, which reduces labor and equipment costs associated with longer curing times. Its ability to set in wet conditions also eliminates the need for dewatering or waiting for dry conditions, saving time and resources.
Overall, the importance of hydraulic cement lies in its ability to provide durable, waterproof, and rapidly setting solutions for various construction and repair projects. Its versatility, strength, and reliable performance make it a valuable material in the construction industry.
How to Use Hydraulic Cement
Using hydraulic cement requires following specific steps to ensure proper application and optimal results. Here’s a general guide on how to use hydraulic cement:
Clean the area: Ensure that the area to be repaired or filled is clean, free from loose debris, dust, oil, or any other contaminants. Use a wire brush or other suitable tools to clean the surface thoroughly.
Wet the area: Before applying hydraulic cement, dampen the area with water. This helps to improve the bonding between the cement and the substrate.
Read the instructions: Follow the manufacturer’s instructions regarding the water-to-cement ratio and mixing procedure. These instructions may vary depending on the specific hydraulic cement product you are using.
Mix in small batches: Prepare only the amount of hydraulic cement that you can use within the specified working time. Mixing small batches ensures that the cement remains workable during application.
Apply the cement: Using a trowel or a suitable tool, apply the mixed hydraulic cement to the prepared area. Press the cement firmly into the crack or void, ensuring that it completely fills the space. Smooth the surface of the applied cement to make it level with the surrounding area.
Work quickly: Hydraulic cement typically sets and hardens rapidly, so it’s important to work efficiently and complete the application within the recommended time frame.
Build-up layers if necessary: For larger repairs or deep voids, it may be necessary to apply hydraulic cement in multiple layers, allowing each layer to partially set before applying the next.
Types of Hydraulic Cement
Keep the area moist: After applying hydraulic cement, it’s crucial to keep the repaired area moist during the curing process. This can be done by misting the surface with water or covering it with a damp cloth. Moisture helps promote proper hydration and strength development.
Follow curing time: Allow the hydraulic cement to cure for the recommended time specified by the manufacturer. This ensures that the cement achieves its full strength and durability.
Note: It’s important to carefully read and follow the specific instructions provided by the manufacturer of the hydraulic cement you are using. Different products may have variations in mixing ratios, working times, and curing requirements.
Additionally, if you are unsure about the application process or dealing with complex repairs, it is advisable to consult a professional or seek expert guidance to ensure proper use of hydraulic cement.
There are several types of hydraulic cement available, each with its own specific characteristics and applications. Here are some common types of hydraulic cement:
Portland Cement
Portland cement is the most widely used type of hydraulic cement. It is produced by grinding clinker, a mixture of limestone, clay, and other materials, and adding a small amount of gypsum. Portland cement is versatile and can be used in a wide range of construction projects, including the construction of buildings, bridges, roads, pavements, and more. It provides strength, durability, and excellent bonding properties when properly mixed with water and aggregate
White Hydraulic Cement
This type of hydraulic cement that is formulated to produce a white or light-colored finish. It is commonly used in applications where aesthetic appeal is important, such as architectural concrete, decorative elements, and other projects that require a bright white appearance.
White hydraulic cement is manufactured similarly to ordinary Portland cement, but it uses raw materials that produce a lighter color, such as white limestone, white clay, or gypsum.
Moderate Heat of Hydration Hydraulic Cement
This type of hydraulic cement that produces a moderate amount of heat during the hydration process. Heat of hydration is the heat generated when cement reacts chemically with water to form solid compounds.
Moderate heat of hydration cement is designed to reduce the heat generated compared to regular hydraulic cement, which can produce significant heat during the hydration process. This controlled heat generation is beneficial in certain situations where excessive heat can cause problems, such as thermal cracking or loss of strength.
It is commonly used in large concrete placements where the size or thickness of the concrete element, the ambient conditions, or other factors make controlling heat buildup important. Examples of such applications include massive concrete structures, dams, bridges, and certain types of foundations.
High Early Strength Hydraulic Cement
High early strength hydraulic cement, also known as rapid-setting hydraulic cement, is a type of hydraulic cement that develops strength rapidly after its initial setting. It is designed to achieve higher strength in a shorter period compared to standard hydraulic cement.
Low Heat of Hydration Hydraulic Cement
Low heat of hydration hydraulic cement is a type of cement that generates less heat during the hydration process compared to standard hydraulic cement. Heat of hydration refers to the heat released when cement reacts with water to form solid compounds.
Low heat of hydration cement is specifically formulated to reduce the heat generated during hydration. This controlled heat generation is beneficial in situations where excessive heat can cause issues such as thermal cracking, shrinkage, or damage to sensitive structures.
It is commonly used in large-scale concrete projects where controlling heat buildup is critical. It is particularly suitable for massive concrete structures, such as dams, thick foundations, and high-rise buildings, where temperature differentials can cause thermal stresses and potential cracking.
Moderate Sulfate-Resistant Hydraulic Cement (MSRHC)
This type of hydraulic cement specifically designed to provide moderate sulfate resistance in environments where exposure to sulfates is a concern. Sulfate attack can occur when sulfates in the soil or water react with the components of concrete, leading to the deterioration of concrete structures over time. MSRHC is formulated to mitigate the effects of sulfate attack and maintain the long-term durability of concrete.
MSRHC is commonly used in construction projects where exposure to sulfates is anticipated. This includes areas with high sulfate concentrations in the soil, groundwater, or marine environments. It is frequently utilized in the construction of foundations, retaining walls, sewage treatment plants, coastal structures, and other infrastructure exposed to sulfate-containing substances.
MSRHC is commonly used in construction projects where the concrete structures are exposed to sulfate-rich environments. It is suitable for applications such as foundations, underground structures, wastewater treatment plants, marine structures, and other areas where exposure to sulfates is expected.
Uses of Hydraulic Cement
Hydraulic cement is widely used in various construction and repair applications due to its unique properties. Some common uses of hydraulic cement include:
Hydraulic cement is widely used to repair cracks and gaps in foundation walls as well as secure bolts and other equipment to the foundation.
Hydraulic cement is frequently used to repair concrete constructions such as bridges, dams, and buildings that have been damaged. It can fill the concrete’s fractures, flaws, and other gaps.
Hydraulic cement is frequently utilized in the construction of roads and bridges. It produces a robust, long-lasting concrete mixture that can withstand heavy traffic and other environmental variables.
Tunnels and underground structures
Hydraulic cement is frequently utilized in tunnel and underground structure construction. It forms a robust, waterproof seal around pipes, cables, and other penetrating objects.
Hydraulic cement is utilized in the construction of docks, piers, and other marine structures. It can be used to seal cracks and holes in concrete and to form a waterproof seal around piles.
Products made from pre-cast concrete, such as pipes, blocks, and panels, are produced using hydraulic cement.
Hydraulic cement is an excellent waterproofing material. It can be used to build a waterproof barrier on basement walls and floors, as well as swimming pools and other exposed structures.
Advantages of Hydraulic Cement
Hydraulic cement offers several advantages that make it a preferred choice in various construction and repair applications. Here are some of the key advantages of hydraulic cement:
- Ability to set and harden underwater, making it suitable for underwater construction and repairs.
- Rapid setting time, allowing for quick repairs and time-sensitive projects.
- Strong and durable bond, providing excellent compressive strength and long-term durability.
- Water-resistant properties, effectively sealing cracks and preventing water infiltration.
- Versatility, applicable to various surfaces and used in a wide range of construction projects.
- Compatibility with other materials, ensuring seamless integration with existing structures.
- Ease of application, with user-friendly forms available for convenient mixing and use
- Cost-effective solution, reducing labor costs and minimizing the need for frequent repairs or replacements.
Disadvantages of Hydraulic Cement
Limited working time: Hydraulic cement typically has a short working time, meaning it must be mixed, applied, and finished quickly. This can be challenging, especially for larger or more complex projects, requiring efficient planning and execution.
Mixing and application considerations: Hydraulic cement requires proper mixing and application techniques to ensure consistent and reliable results. Incorrect proportions of water or inadequate mixing can lead to weakened or compromised strength and performance.
Temperature sensitivity: The setting and curing process of hydraulic cement can be influenced by temperature. Extreme heat or cold temperatures can affect the setting time, strength development, and overall performance of the cement. Special considerations and precautions may be necessary in extreme temperature conditions.
Shrinkage: Hydraulic cement can undergo some shrinkage during the drying and curing process. This can lead to the development of small cracks or gaps in the material, especially if the application is not properly controlled or the mixture is not proportioned correctly.
Environmental Impact: Due to the high energy requirements for hydraulic cement manufacture, there may be environmental issues such as greenhouse gas emissions. The cement may also contain heavy metals and other contaminants that can contaminate the environment.