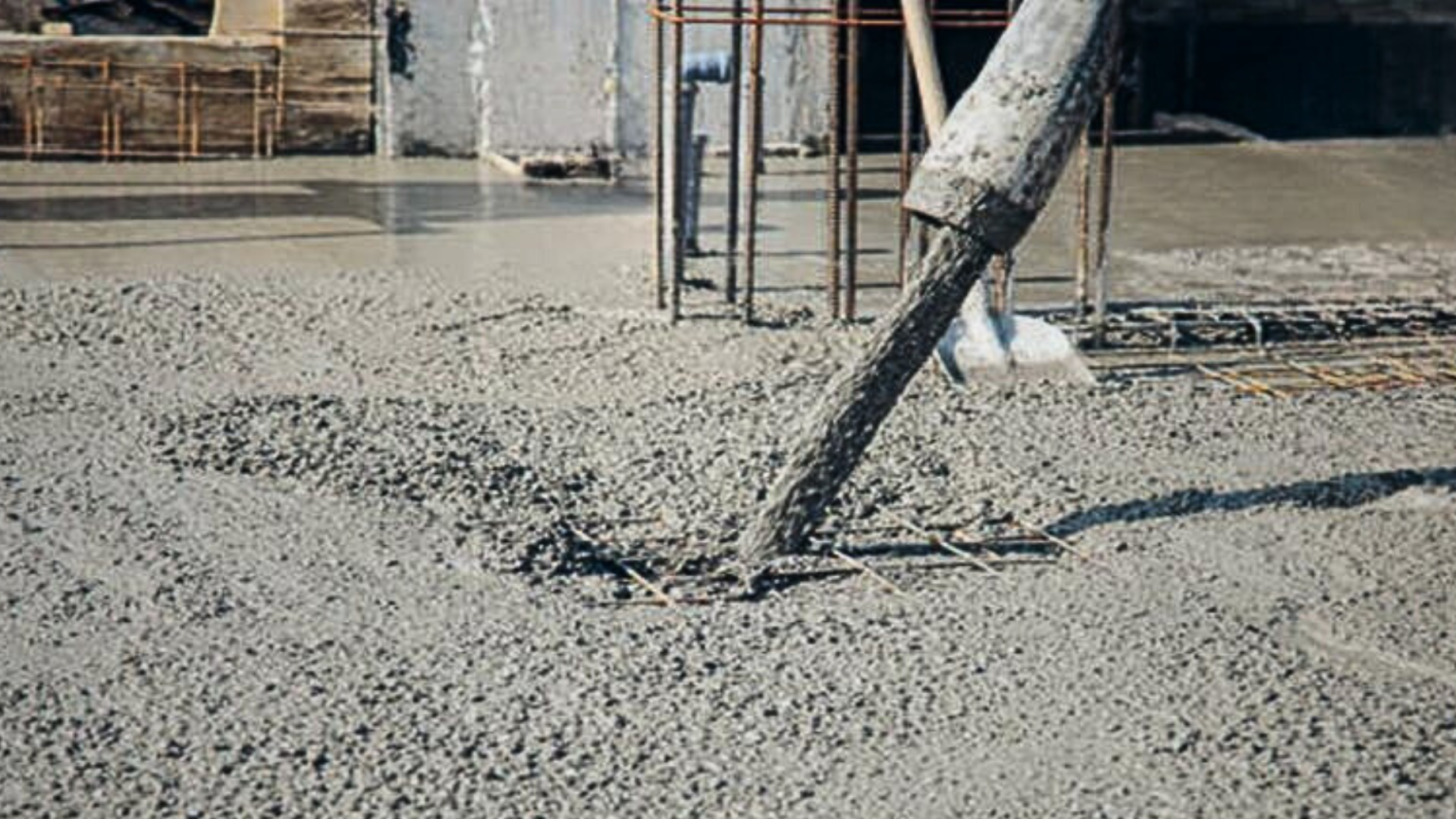
In this article, we will delve into the factors affecting the pumpability of concrete. The pumpability of concrete refers to the ease with which fresh concrete can be transported and placed in the formwork using a concrete pump. Several factors can influence the pumpability of concrete, and understanding these can help in producing concrete that is easy to pump, reducing the risk of blockages and ensuring a smooth and efficient process.
Factors Affecting Concrete Pumpability
Pumpable concrete is a specialized type of concrete that can be transferred to significant heights through pipes. It is commonly used when a large volume of concrete needs to be placed in a specific location. The pumpability of concrete is influenced by various factors, including the types of cementitious materials, characteristics of the aggregates, admixtures used, and the batching and mixing process.
The choice of cementitious materials can have a positive impact on the pumpability of concrete. Materials such as fly ash and silica fumes can improve the flowability and workability of the concrete, making it easier to pump. It is important to consider the maximum aggregate size in relation to the diameter of the pumping pipes. Generally, the maximum aggregate size should not exceed one-quarter of the pipe diameter to prevent blockages or difficulties in pumping.
When using pumpable concrete, it is crucial to take precautions when incorporating lightweight or heavyweight aggregates. These types of aggregates can affect the pumpability of the concrete, so their use should be carefully considered and appropriate adjustments made to the mix design.
Accurate and proper batching and mixing of the concrete constituents are essential for achieving good pumpability. The proportions of the materials should be measured accurately, and the mixing process should be thorough to ensure a homogeneous mixture. Inadequate batching or mixing can result in issues during concrete pumping, such as blockages, segregation, or reduced flowability.
To avoid potential problems during concrete pumping, it is important to follow industry best practices and guidelines. This includes selecting the appropriate cementitious materials, considering the aggregate characteristics, and ensuring accurate batching and mixing of the concrete constituents. By paying attention to these factors, the pumpability of the concrete can be optimized, leading to successful and efficient concrete placement.
What are the Factors Affecting Pumpability of Concrete?
The pumpability of concrete refers to its ability to flow smoothly and easily through a concrete pump. Several factors can affect the pumpability of concrete. Here are some key factors to consider:
A. Cementitious Materials
Fine cement is typically used to prevent pumped concrete from bleeding, which is a serious issue that must be avoided. Thus, the better the cement, the finer it is.
The use of fly ash in pumped concrete is highly advantageous since its spherical particles and glassy texture improve mixture cohesion and reduce the amount of water required for mixing.
Another additive for improving concrete pumpability is silica fume. Furthermore, it makes the concrete mixture much more cohesive.
Furthermore, because the shape and texture of its particles are comparable to Portland cement, ground granulated blast furnace slag could slightly improve concrete pumpability.
However, if a high amount of ground-granulated blast furnace slag is utilized in a mixture containing heavyweight aggregates, concrete segregation is likely. Also, adding ground-granulated blast furnace slag delays the setting time of concrete, which may be advantageous in some situations.
Similar to ground-granulated blast furnace slag, metakaolin is used in low-cohesion concrete but has no discernible or significant effect on the pumpability of the material.
Also Read:
- Box culvert reinforcement lay-out
- Method and Period of Formwork Removal
- Concrete Stairs Reinforcement Details
- Concrete Curing
- Concrete Pumps
- Stamped Concrete
B. Aggregate Characteristics
Several factors can affect the pumpability of concrete, which refers to its ability to flow smoothly through a concrete pump without blockages or excessive pressure. Here are some factors related to aggregate characteristics that can impact pumpability:
The size of aggregates plays a crucial role in the pumpability of concrete. Smaller aggregates, such as fine sand, tend to have better pumpability compared to larger aggregates. This is because smaller aggregates can flow more easily through the pumping system without clogging or causing blockages. It is important to use aggregates of an appropriate size that can pass through the pump without causing any issues.
The grading of aggregates refers to the distribution of particle sizes within the aggregate mixture. Well-graded aggregates with a balanced distribution of different sizes are generally more pumpable. This is because the presence of different-sized particles allows for better packing and reduces the likelihood of segregation during pumping.
The shape of aggregates can also affect the pumpability of concrete. Angular aggregates with rough surfaces tend to interlock better, making them more difficult to pump. On the other hand, rounded aggregates with smoother surfaces can flow more easily through the pumping system. It is important to consider the shape of aggregates and choose those that are more suitable for pumping applications.
The density of aggregates can impact the pumpability of concrete to some extent. Aggregates with higher density, such as heavyweight aggregates, may require more pumping pressure to move through the system. However, the overall pumpability is influenced more by the size, grading, and shape of the aggregates rather than their density.
C. Admixture
The use of admixtures in concrete can also affect its pumpability. Admixtures are chemical additives that are added to the concrete mix to modify its properties. Here are some admixture factors that can impact the pumpability of concrete:
Water-reducing admixtures are beneficial for improving pumpability. By reducing the amount of free water in the mix, these admixtures help prevent excessive bleeding and segregation. They also enhance workability, allowing the concrete to flow more easily through the pump without clogging or blockages.
High-Range Water-Reducing Admixtures (Superplasticizers
High-range water-reducing admixtures, also known as superplasticizers, are particularly effective in enhancing pumpability. These admixtures can greatly reduce the water content in the mix while maintaining workability. By providing better flowability, superplasticizers enable the concrete to move smoothly through the pump and reach its intended destination.
Air-entraining admixtures improve the cohesion and pumpability of concrete. They create small, evenly distributed air bubbles in the mix, which enhance its workability and flow characteristics. However, it’s important to note that the benefits of air-entraining admixtures may be limited if the cement content of the mixture is already high.
Retarder admixtures are useful in hot environments or situations where unexpected delays occur. These admixtures slow down the setting time of concrete, providing more workability and extending the time available for concrete placement. By allowing for a longer working time, retarders can contribute to improved pumpability, especially in challenging conditions.
D. Material Batching and Mixing
Pumpable concrete is significantly influenced by inaccuracies in batching, the amount of mixing water, and other potential errors that can occur during material batching. Hence, precise concrete batching is essential to ensure pumpable concrete.
When it comes to material mixing, it is crucial to mix pumpable concrete thoroughly, and the machinery utilized for this task should be operated according to the manufacturer’s guidelines. Lastly, it is recommended to remix ready-mix concrete before it is loaded into the pump.