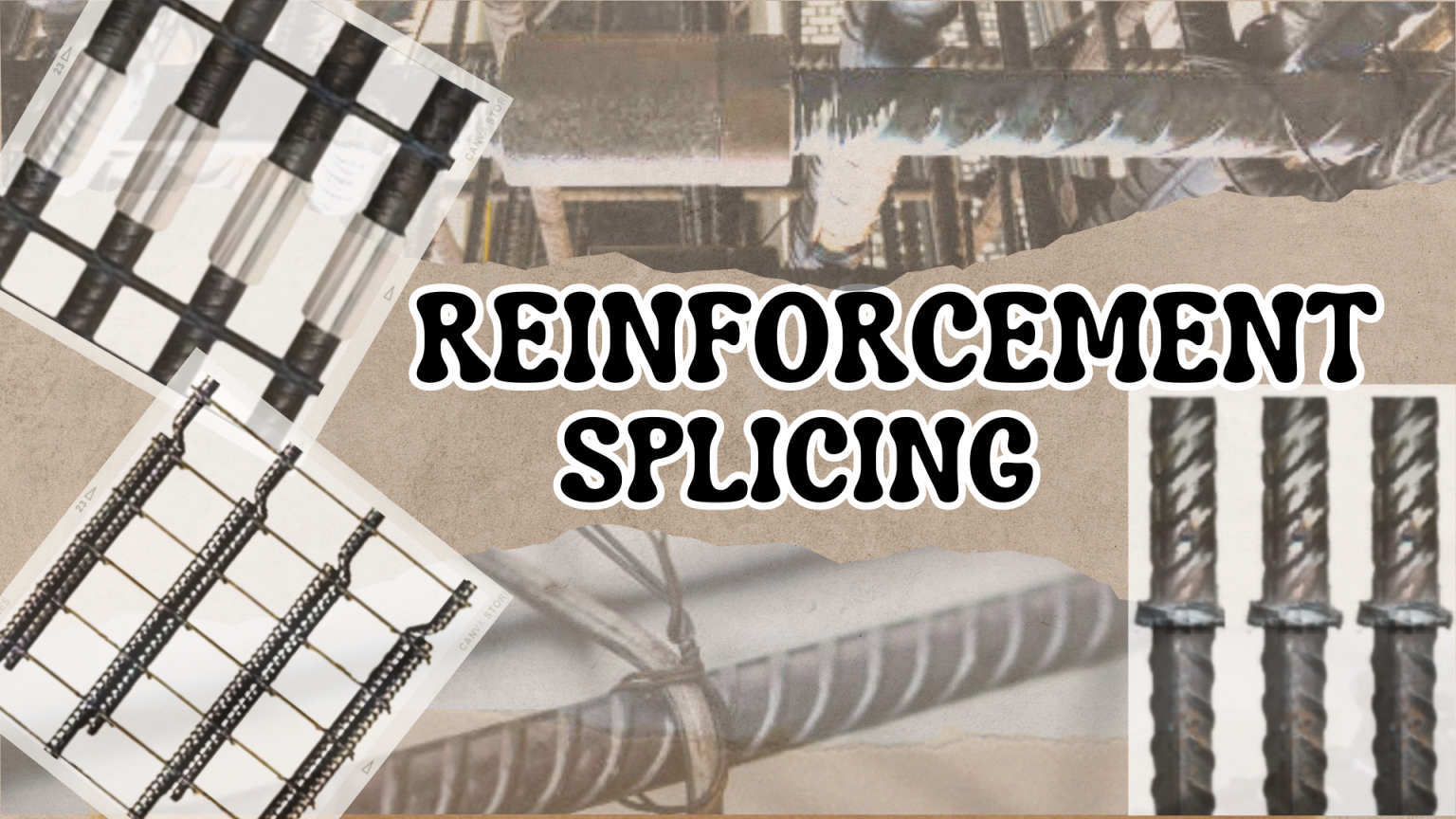
Reinforcement splicing, also known as rebar splicing, is the process of connecting two or more reinforcing bars (rebars) to create a continuous reinforcement in reinforced concrete structures. Reinforcement splicing is typically done to achieve structural integrity, continuity, and load transfer across the spliced bars. Proper reinforcement splicing is critical to ensure the performance and durability of reinforced concrete structures.
There are various methods for reinforcement splicing, including:
Mechanical Splicing
Mechanical splicing involves using mechanical devices, such as couplers or connectors, to join the rebars together. Mechanical splicing methods typically involve threaded, tapered, or other types of couplers that are attached to the ends of the rebars, and then tightened or connected using tools or equipment. Mechanical splicing provides a fast, efficient, and reliable way to join rebars without the need for welding or lapping, and it maintains the continuity of reinforcement along the length of the structure.
Welded Splicing
Welded splicing involves welding the ends of the rebars together to create a continuous reinforcement. This method requires skilled welders and proper welding procedures to ensure the quality and integrity of the weld. Welded splicing is commonly used in applications where high load transfer capacity and structural performance are required, but it may not be suitable for all situations due to the need for skilled labor, welding equipment, and potential limitations related to site conditions or environmental factors.
Lap Splicing
Lap splicing involves overlapping the ends of the rebars and securing them with wire or other types of connectors. Lap splicing is a traditional and commonly used method of reinforcement splicing, but it may require longer lengths of rebars compared to mechanical splicing or welded splicing, as the overlapping lengths need to meet certain design requirements for proper load transfer.
Rebar Coupler vs Welding vs Lapping
When it comes to connecting reinforcing steel bars (rebars) in construction, there are three main methods: rebar couplers, welding, and lapping. Each method has its advantages and disadvantages, and the best choice depends on various factors, such as the project requirements, the available equipment and tools, the experience of the workers, and the budget.
Rebar Couplers
Rebar couplers, also known as mechanical splices are mechanical connectors that join two rebars end-to-end without the need for threading or welding. They are made of steel sleeves that are threaded internally and externally and are installed on the ends of the rebars by screwing them together using a torque wrench. This method is faster, safer, and more reliable than traditional lap splicing, which requires longer lap lengths and is more labor-intensive.
Mechanical couplers are the most popular mechanical splice or joint used for reinforcement. There are two different types of mechanical couplers:
- Threaded Couplers
- Non-threaded couplers
A.Threaded Couplers
There are two types of threaded couplers:
1. Tapered Threaded Couplers
This type of tapered coupler is fitted to one end of the threaded rebar, attached, and tightened with a calibrated torque wrench. This procedure is performed at the site.
2. Roll Threaded Couplers
In this type, the bars to be joined are pressed by a set of rollers. These pressed ends are joined by couplers with matching and parallel threads.
B. Non – Threaded Couplers
There are various varieties of this coupler type that are utilized in places where threaded couplers cannot be used. The various types are as follows:
- Bolted Couplers
- Friction weld couplers
- Swage Couplers
- Welded Couplers
Bolted Couplers
Bolted couplers use bolts to secure the connection between the reinforcement bars. The coupler has two halves, and the bar ends are inserted into each half. Bolts are then used to tighten the halves together, creating a tight and secure connection. Bolted couplers are commonly used in precast concrete construction.
Friction Weld Couplers
Friction welded couplers use friction welding to join the reinforcement bars together. The bar ends are inserted into the coupler, and then the coupler is rotated at high speed while pressure is applied to create friction heat. The heat fuses the bar ends together, creating a strong and permanent connection.
Swaged Couplers
Swaged couplers are couplers that are deformed or swaged onto the reinforcing bars. This creates a mechanical grip between the coupler and the bars, providing a strong and reliable connection.
Welded Couplers
Weldable couplers allow for the reinforcement bars to be welded to the coupler, creating a strong and permanent connection. Weldable couplers are commonly used in high-rise buildings, bridges, and other structures where a high level of strength and stability is required.
Advantages of Rebar Coupler / Mechanical Splices
Faster installation: Rebar couplers eliminate the need for cutting and threading of the rebars, which saves time and labor costs.
High strength: Coupled rebars have similar or even higher strength than the original rebars, and the connection is not affected by the quality of the weld or the accuracy of the lap length.
Space-saving: Couplers require less space than lap splices, which is important in congested reinforcement areas.
Safer: Couplers eliminate the need for onsite welding, which can be a fire hazard and cause health and safety concerns
Disadvantages of Rebar Coupler / Mechanical Splices
Cost: Rebar couplers are more expensive than lap splicing due to the cost of the coupler itself and the specialized equipment needed for installation.
Specialized equipment: Installation requires a torque wrench, a portable power unit, and other specialized equipment that may not be available onsite.
Quality control: Installation must be performed by trained and certified workers, and proper quality control measures must be in place to ensure proper installation.
Also Read: Types of Brazing Method | Fiber Reinforced Concrete | Box Culvert Reinforcement Layout | Types of Rebar
Welded Splice
Welding is a common method for joining rebars, where the ends of the rebars are welded together using an electric arc welding process. Welded splices can provide a strong and continuous connection that is not affected by the environment or external forces.
Note: Only wedlable rebar should be used because not all rebars are wedlable.
Advantages of Welding
High strength: Welded splices provide a strong and continuous connection that has similar or even higher strength than the original rebars.
Durable: Welded splices are not affected by the environment or external forces and can last a long time.
Suitable for all reinforcement sizes: Welding can be used for all sizes of reinforcement bars.
Disadvantages of Welding
Health and safety concerns: Welding can be a fire hazard and cause health and safety concerns if proper precautions are not taken.
Cost: Welding requires specialized equipment and qualified workers, which can add to the cost of the project.
Quality control: Welding requires high-quality workmanship and proper quality control measures to ensure that the connection is strong and durable.
Limited space: Welding requires more space than couplers or lap splices, which may not be available in congested reinforcement areas.
Lap Splice
Lapping is the traditional method of joining rebars, where the two rebars overlap and are tied together using wire or other methods. Lap splices require longer lap lengths to achieve the same strength as coupled or welded splices and are more labor-intensive.
Advantages of Lapping
Low cost: Lap splices are the least expensive method of joining rebars, as they require only basic tools and materials.
No specialized equipment needed: Lap splices do not require any specialized equipment or trained workers, making them accessible to small construction projects or DIY enthusiasts.
Disadvantages of Lapping
High labor costs: Lap splices require longer lap lengths to achieve the same strength as coupled or welded splices, which can be more labor-intensive and time-consuming.
Quality control: Lap splices require high-quality workmanship and proper quality
Rebar Coupler vs Welding vs Lapping
COUPLING | WELDING | LAPPING | |
---|---|---|---|
Load Transfer | Great | Depends on concrete | Depends on concrete |
Load Path Continuity | Accurate | Not good | Not good |
Structural Integrity | Great | Moderate | Moderate |
Rebar Congestion | Rebar couplers do not cause congestion | Create congestion, make concrete pouring difficult, and vibration. | Create congestion, make concrete pouring difficult, and vibration. |
Steel Quantity | Less | Requires extra steel for welding | Requires extra steel for lapping |
Splice Calculation | Not required | — | Required |
Quality Control | Great | Low to medium | Moderate |
Supervising | Easy | Not easy | Easy |
Wastages | Minimal | High | High |