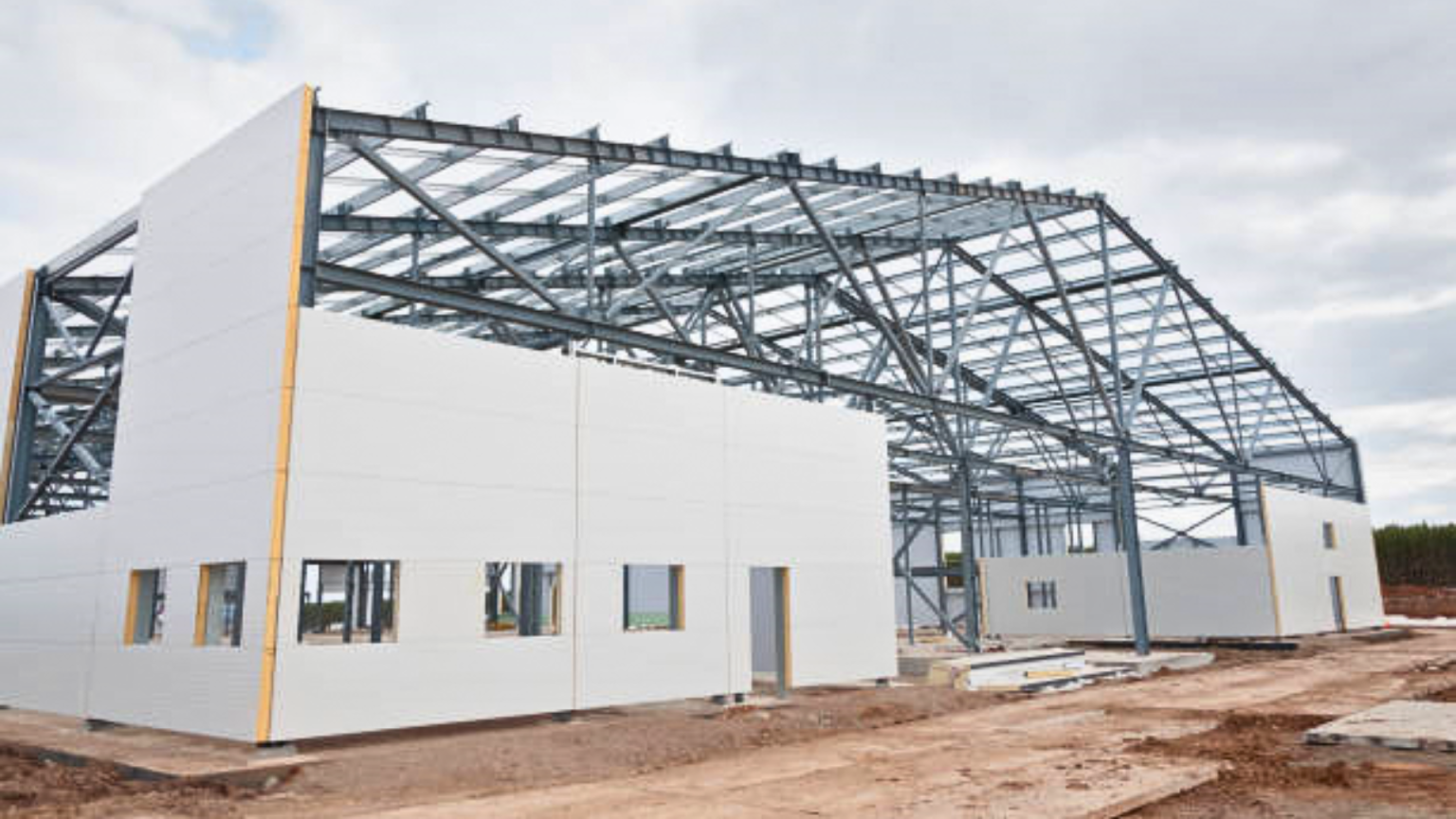
A Pre-engineered Building (PEB) is a construction method where structural components are manufactured in a factory and then assembled on-site. This approach is characterized by the use of standardized and prefabricated elements, which are designed and fabricated using advanced techniques and technology. The components are typically made of steel and are engineered to meet specific design criteria, providing a cost-effective and efficient solution for a variety of structures.
Components of Pre-Engineered Building
A pre-engineered building (PEB) is composed of several key components that are designed and fabricated off-site before being transported to the construction site for assembly. The specific components can vary based on the design and purpose of the building, but here are some common elements:
Primary Frame
Trusses, column or castellated beams, and other structural elements consist of primary frames. These are constructed from I-shaped steel components. The load of all structure members passes to the foundation, which is made up of end-wall frames.
These end-wall frames are built with either robust or economical bearing frames. Wind bracing and connecting bolts reinforce these frames. Sometimes anchor bolts are used.
Secondary Components
Secondary elements are cold-formed structural parts available in various shapes such as C, Z, and so on—commonly known as “Purlins.” These purlins transfer force from one frame to another for overall structure stability.
These purlins are corrosion-resistant, strong, lightweight, and simple to install. Purlins are available in a variety of lengths and thicknesses.
Roof and wall panels
Some pre-engineered building components, such as roof and wall panels, are available in tin shades and curtain walls made of glass and roll-formed steel sheets. Special roofing sheets are utilized to save electricity.
Sandwich Panels
These panels are three-layered, with one non-aluminum layer sandwiched between two aluminum sheets.
Sandwich panels also include bolts, insulation, mezzanine flooring, skylight sheets, flashlights, cage ladders, cable trays, ducts, cranes, and other components.
Advantages and Disadvantages of Pre-Engineered Building (PEBs)
Advantages
Cost-Effective Construction
PEBs are generally more cost-effective than traditional construction methods due to reduced labor costs, faster construction timelines, and efficient use of materials.
Speed of Construction
PEBs are designed for quick and easy assembly since components are pre-engineered and prefabricated. This can lead to significantly faster construction times compared to conventional buildings.
Design Flexibility
PEBs can be customized to meet specific design requirements and can be adapted for various uses, such as warehouses, factories, offices, and recreational facilities.
Quality Control
Components are fabricated in a controlled factory environment, allowing for strict quality control measures. This helps ensure that each component meets the required standards.
Energy Efficiency
PEBs can incorporate energy-efficient features, such as insulation, natural lighting, and ventilation systems, contributing to energy savings over the life of the building.
Versatility
The modular nature of pre-engineered building components allows for easy expansion or modification of the structure to accommodate changing needs.
Reduced Waste
The precision of the manufacturing process and the use of optimized materials help minimize waste during construction.
Structural Strength
PEBs are designed to meet specific structural requirements, providing strength and stability suitable for a variety of applications.
Also Read:
- Demolition Techniques
- Method and Period of Formwork Removal
- Plastering: Purpose and Types of Plaster Finishes
- Concrete Spalling: Causes and How It Can Be Prevented
Disadvantages
Limited Height
In some cases, the height of a pre-engineered building may be limited compared to traditional construction methods.
Limited Aesthetic Options
PEBs may have limitations in terms of architectural aesthetics compared to traditional construction methods, which might be a consideration for certain projects.
Transportation Costs
Transportation costs can be a factor, especially for large or complex structures. The prefabricated components need to be transported to the construction site.
Prone to Corrosion
Corrosion can be a concern in pre-engineered buildings (PEBs), especially if the materials used in the construction are susceptible to corrosion.
Material Susceptibility
Many pre-engineered building components, such as steel columns, beams, and fasteners, are susceptible to corrosion when exposed to harsh environmental conditions, especially in coastal or industrial areas where there is a high presence of salt or other corrosive agents.
Maintenance Requirements
Regular maintenance may be required to inspect for and address any signs of corrosion. This can include applying protective coatings or paints, which adds to the ongoing maintenance costs of the building.
Potential for Structural Damage
Corrosion can compromise the structural integrity of metal components over time. If not addressed, it can lead to weakening of the structure, affecting its load-bearing capacity and safety.
Reduced Lifespan
Corrosion can accelerate the aging process of metal components, potentially reducing the overall lifespan of the pre-engineered building. This is a concern if the building is intended for long-term use without significant structural upgrades.
Cost of Corrosion Protection
Incorporating corrosion-resistant materials and protective coatings can increase the initial cost of a pre-engineered building. While this cost may be justified in corrosive environments, it adds to the overall project expenses.
Environmental Factors
Factors such as humidity, exposure to saltwater, industrial pollutants, and other environmental conditions can accelerate the corrosion process, making it necessary to carefully consider the building’s location and the materials used.
Application of Pre-Engineered Building
- Factories
- Workshops
- Offices
- Warehouses
- Showrooms
- Gas Stations
- Vehicle Parking Sheds
- Metro Stations
- Aircraft Hangars
- Schools
- Recreational
- Bridges
- Indoor Stadium Roofs
- Outdoor Stadium Canopies
- Railway Platform Shelters
Difference between Pre-Engineered Building and Conventional Steel Building
PROPERTIES | PRE-ENGINEERED BUILDING | CONVENTIONAL STEEL BUILDING |
---|---|---|
Design Process | PEBs undergo a design process where the building components are pre-designed and standardized. The design is often done using computer-aided design (CAD) software, and the components are manufactured off-site. | Conventional steel buildings involve a more traditional design process where each component is individually designed by architects and engineers. The design is usually more customized to meet specific project requirements. |
Manufacturing and Fabrication | Components of PEBs, such as columns, beams, and panels, are fabricated off-site in a controlled factory environment. The components are then shipped to the construction site for assembly. | In conventional steel construction, most of the fabrication work is done on-site. Steel beams, columns, and other elements are cut, welded, and assembled at the construction site. |
Construction Time | PEBs are known for their faster construction time compared to conventional buildings. The prefabricated components are designed for quick and easy assembly on-site, leading to shorter construction schedules. | Conventional steel buildings may have longer construction times due to the on-site fabrication and assembly processes, which are generally more labor-intensive. |
Customization | While PEBs offer some degree of customization, they are often more standardized in design. Customization options may be limited compared to conventional construction. | Conventional steel buildings allow for greater customization in terms of architectural design, which can be important for projects with specific aesthetic or functional requirements. |
Cost | PEBs are often more cost-effective in terms of material usage, labor, and construction time. The standardized components and streamlined design contribute to cost savings. | Conventional steel buildings may involve higher costs due to the customized design, on-site fabrication, and potentially longer construction timelines. |
Size and Complexity | PEBs are well-suited for projects with clear spans and straightforward designs. They may be less suitable for highly complex or architecturally intricate structures. | Conventional steel construction can handle a wide range of project sizes and complexities, making it more suitable for projects with unique design requirements. |
Versatility | PEBs are versatile and suitable for a variety of applications, including warehouses, industrial buildings, and commercial structures. | Conventional steel buildings are also versatile and can be adapted to a wide range of applications, including complex architectural designs. |
Architecture | An outstanding architectural design can be produced with the help of standard design features. | Special design is required for various tasks, which results in expensive costs. |
Future Expansion | Any future extension will be easy and simple. | Future expansion may be more expensive and time-consuming in this matter. |
Foundation | Due to their lightweight nature, they have an easy-to-use design and can be constructed quickly. | In traditional construction, a broad and massive foundation is necessary. |
Seismic Resistance | Lightweight frames provide greater resilience to seismic stresses in pre-engineered buildings. | Conventional building systems with rigid, heavy frames are less resistant to seismic forces. |
Performance | All components have been specifically developed and built to work as a system for maximum efficiency, accuracy, and optimal performance in the field. | Components are built specifically for a specific use on a given job. When integrating the various components into distinct buildings, design and detail faults are conceivable. |
Safety and Responsibility | Since the entire job is being done by one supplier, there is a single point of contact. | Multiple roles can lead to confusion about who is liable when components do not fit well, insufficient material is given, or parts fail to work, particularly at the supplier/contractor interface. |